“如何配置一条高效的花岗岩破碎生产线,既能满足粗碎需求,又能产出高价值的精品砂石?”——这是许多砂石厂商、矿山管理者和工程承包商在项目初期最头疼的问题。花岗岩因其高硬度和高耐磨性,对破碎设备的性能、工艺流程的科学性提出了严苛要求。然而,现实中因设备选型失误导致的产能瓶颈、成品针片状过多,或是环保不达标被迫停工等问题频繁出现。本文将系统解析花岗岩破碎线的核心配置指南,从粗碎设备选型、中细碎工艺优化,到精品制砂的精细化控制,提供一套经过行业验证的解决方案。
花岗岩破碎线配置指南:
花岗岩破碎难?我们有办法!
花岗岩作为火成岩的典型代表,其莫氏硬度高达6-7级,主要由石英、长石等耐磨矿物构成。这种硬质特性虽赋予其优异的建筑性能应用,却给破碎加工带来三大挑战:
- 高磨损性:石英含量超20%的岩体,对颚板、轧臼壁等部件磨损速度快;
- 能耗与效率矛盾:粗碎阶段需高强度冲击力,但高硬度导致设备功耗飙升;
- 成品粒形控制难:中细碎阶段易产生针片状颗粒,若制砂工艺不当,成品砂粒粒形不达标,直接影响混凝土强度与销售溢价。
如何应对?
对于东能科技来说,一条与花岗岩特性深度匹配的生产线,既是成本控制的防线,更是抢占高端市场的核心武器。我们将科学配置花岗岩破碎生产线,则可最大化制成精品砂:
1. 对抗高磨损:针对性选用耐磨合金材质的颚板、层压破碎的圆锥破,可将关键部件寿命延长2-3倍;
2. 平衡效率与能耗:通过多段破碎工艺,在保证产能的同时,降低吨能耗成本达25%;
3. 工艺优化:采用精细化制砂控制产出高品质精品砂,满足国际混凝土应用标准,提升40%价值。
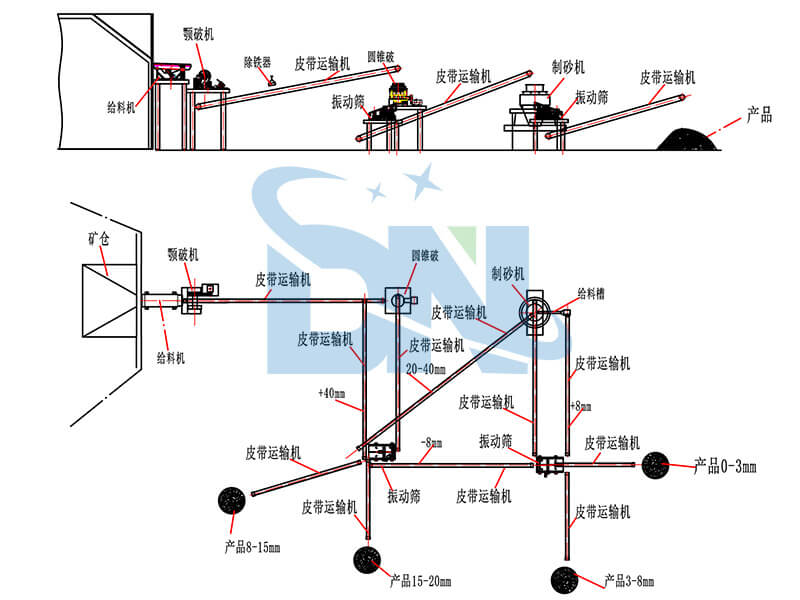
花岗岩破碎生产线分阶段流程
花岗岩作为一种高硬度岩石,其破碎加工需要经过科学的流程设计,以确保成品骨料的粒度与形状满足建筑、道路等工程需求。一条完整的生产线通过从粗砂与精细分选,将坚硬的花岗岩转化为不同规格的建筑骨料。主要包括粗碎、中细碎、筛分、辅助设备及环保处理等关键环节,各阶段紧密配合,直接影响生产效率和环保合规性。
1. 粗碎阶段
花岗岩原矿首先通过振动给料机均匀送入颚式破碎机进行初级破碎。颚破凭借其高强度的破碎腔和楔形调整设计,可将大块花岗岩一次性粉碎至200mm以下的粗料。此阶段需注意设备耐磨件的定期维护,以应对花岗岩的高硬度特性。这一阶段通常首选是颚式破碎机或旋回破碎机。
粗碎设备建议:
颚式破碎机:结构简单、维护便捷,适合中小型生产线(时产≤300吨)。例如C6X系列颚破采用液压调整装置,遇到超大石块或异物时,可快速扩大排料口,避免停机清理,特别适合含土量高或杂质多的矿区。
旋回破碎机:处理能力强大(时产可达2000吨),出料粒度更均匀(90%颗粒<150mm),但初期投资比颚破高30%-40%,更适合大型矿山或对产能要求苛刻的项目。
在花岗岩破碎生产现状中,大部分最常见且常用的粗碎设备是鄂破。选对设备并优化配置,不仅能延长部件寿命,更能为后续中碎、制砂环节的高效运行打下坚实基础。
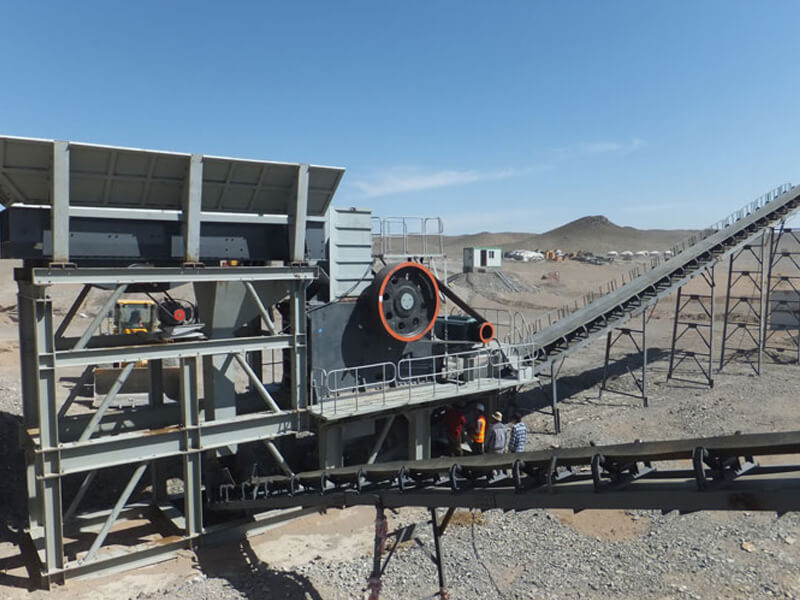
2. 中碎阶段
粗碎后的物料通过皮带机输送到二级破碎设备。中碎阶段的核心目标是将粗碎后的石料加工成均匀的中细骨料。
中碎设备建议:
单缸圆锥破:结构简单、性价比高,适合中小规模生产(时产≤200吨),但耐磨件寿命较短;
多缸液压圆锥破:通过液压系统实时调节排料口,成品中立方体颗粒占比提升至85%以上,且配备过铁保护功能,遇到金属异物时可自动排料,避免主轴断裂事故。
反击式破碎机:花岗岩的高石英成分会加速板锤磨损。因此,反击破针对成品粒形较优,但耐磨件更换更频繁。最好是仅适合加工破碎低硬度岩石(如石灰石)。
若追求颗粒均匀,多选用液压圆锥破碎机,其层压破碎原理能有效减少针片状含量;若需灵活调整成品粒度,反击破或冲击破更为适合,但需权衡耐磨件损耗成本。选择适配的圆锥破型号,配合科学的工艺控制,不仅能降低维护成本,更能让产品溢价能力翻倍。
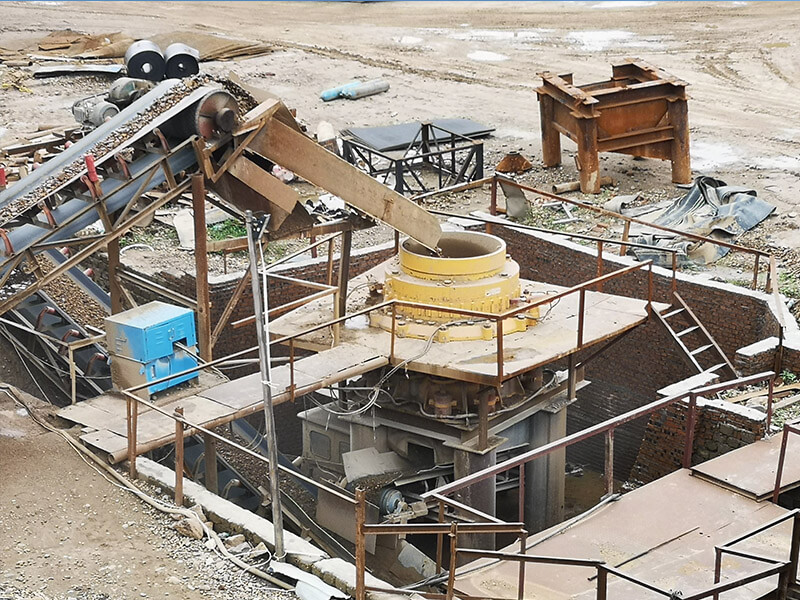
3. 细碎与制砂阶段
细碎与制砂是花岗岩加工的价值跃升环节,核心目标是将3-10mm碎石转化为高附加值的精品砂。
制砂设备建议:
立轴冲击破碎机(VSI):
- 石打石模式:通过石料间碰撞破碎,成品砂粒形圆润(圆度>85%),适合混凝土用砂,但处理量降低15%;
- 石打铁模式:直接冲击周护板,破碎效率提升20%,但针片状颗粒增加,适合路基垫层等低标准场景。
在制砂机前最好是加装振动筛,分离出不符合的粗颗粒返回破碎,减少过粉碎,砂产量提升25%。
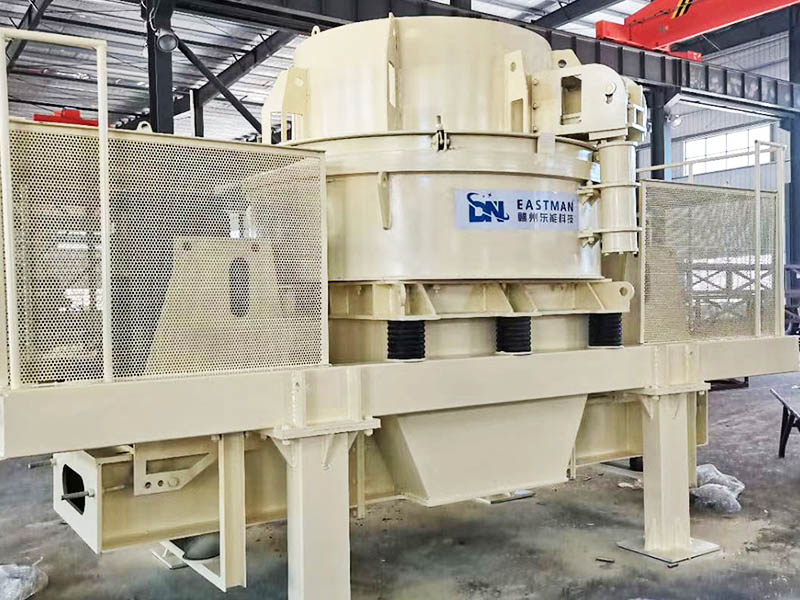
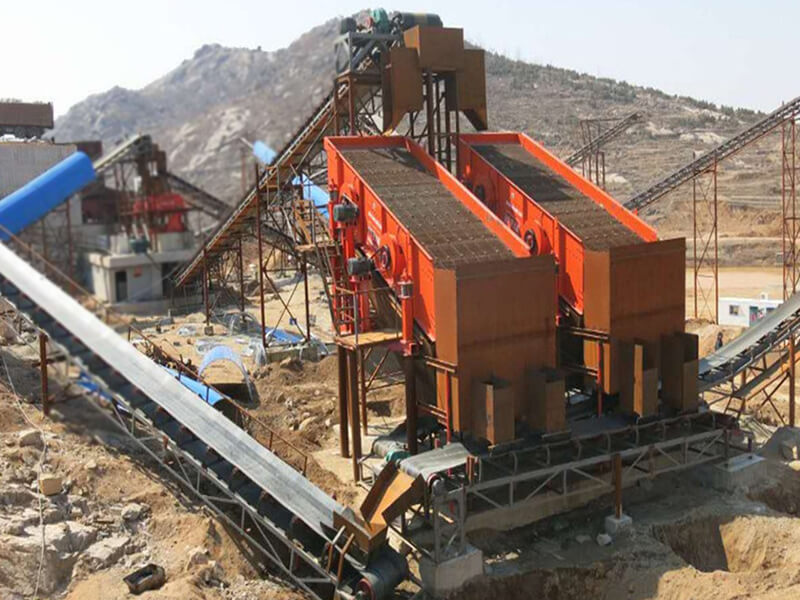